Essential Guide to 12 Inch Wafer Technology and Manufacturing
By:Admin
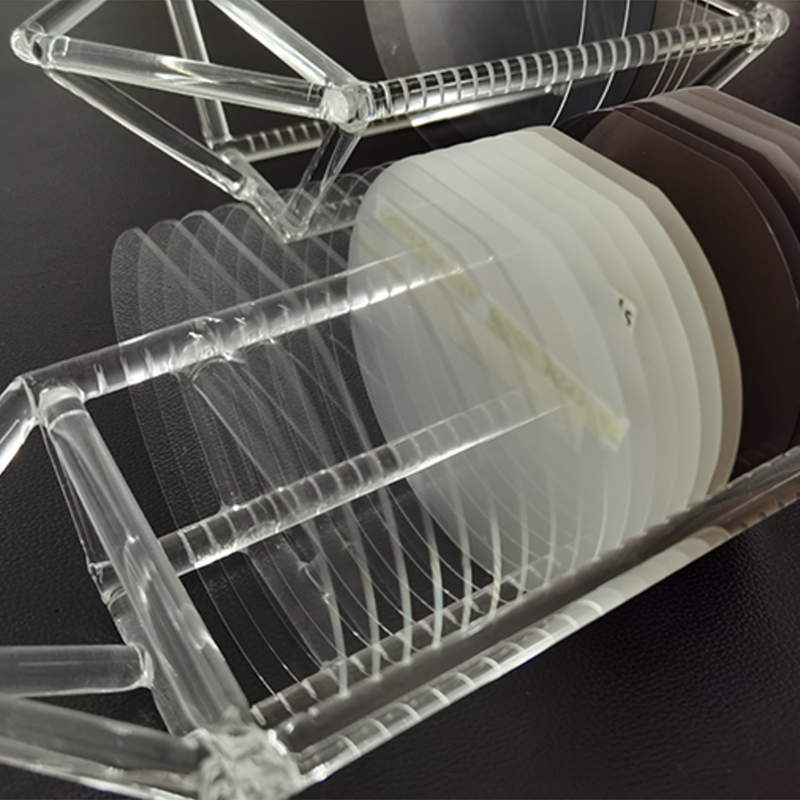
In the rapidly evolving world of technology, the demand for smaller, faster, and more powerful electronic devices continues to drive innovation in the semiconductor industry. As a key player in this field, {company name} has recently achieved a significant milestone with the successful production of 12-inch wafers, marking a major advancement in semiconductor manufacturing.
{Company name} has been at the forefront of semiconductor technology for decades, specializing in the design and production of cutting-edge chips and components for a wide range of electronic devices. With a strong focus on research and development, the company has continuously pushed the boundaries of what is possible in semiconductor manufacturing, driving progress and innovation in the industry.
The transition to 12-inch wafers represents a significant step forward in semiconductor manufacturing, offering a number of important advantages over the traditional 8-inch wafers that have been widely used in the industry. By utilizing larger wafers, {company name} is able to significantly increase the number of chips that can be produced from a single wafer, leading to greater efficiency and cost savings in the manufacturing process. Furthermore, the larger surface area of the 12-inch wafers allows for the development of smaller, more powerful chips, enabling the creation of even more advanced electronic devices.
The successful production of 12-inch wafers is a testament to {company name}'s ongoing commitment to innovation and excellence in semiconductor manufacturing. This achievement would not have been possible without the dedication and expertise of the company's highly skilled team, as well as the ongoing investment in state-of-the-art manufacturing facilities and equipment. By continuously pushing the boundaries of what is possible in semiconductor manufacturing, {company name} is helping to drive progress and innovation in the industry, paving the way for the development of even more advanced electronic devices in the future.
In addition to the immediate benefits of increased efficiency and cost savings, the transition to 12-inch wafers is expected to have a significant long-term impact on the semiconductor industry as a whole. As the industry continues to evolve and demand for smaller, faster, and more powerful electronic devices continues to grow, the ability to produce larger wafers with more advanced chips will become increasingly important. By pioneering the production of 12-inch wafers, {company name} is helping to set new standards for semiconductor manufacturing, positioning itself as a leader in the industry and driving progress and innovation for years to come.
The successful production of 12-inch wafers is a significant achievement for {company name}, one that highlights the company's ongoing commitment to excellence and innovation in semiconductor manufacturing. By pushing the boundaries of what is possible in the industry, the company is helping to drive progress and innovation in the semiconductor industry, paving the way for the development of even more advanced electronic devices in the future. With this milestone, {company name} is well positioned to continue leading the way in semiconductor technology, setting new standards for manufacturing and driving progress and innovation for years to come.
Company News & Blog
Durable Fused Silica Substrate Technology: What You Need to Know
Fused Silica Substrate is a critical component in the manufacturing of various high-tech products, and one company leading the way in producing this essential material is {}. {} is a global leader in the development and production of advanced materials and solutions for a wide range of industries, including electronics, telecommunications, and aerospace. The company has a proven track record of delivering high-quality products and has established itself as a trusted partner for many leading companies around the world.Fused silica is a type of glass that is made from high-purity silica sand, which is melted and then solidified to form a transparent and highly durable material. It is known for its excellent thermal stability, low thermal expansion, and high optical transmission, making it an ideal substrate for a variety of applications. {} has developed advanced manufacturing processes to produce fused silica substrates with precise dimensions and superior optical and mechanical properties, meeting the stringent requirements of its customers.One of the key applications of fused silica substrates is in the production of semiconductor devices. As the semiconductor industry continues to advance, there is a growing demand for high-quality substrates that can meet the increasing performance and reliability requirements of advanced electronic devices. {} has been at the forefront of meeting this demand by developing fused silica substrates that enable the production of cutting-edge semiconductor devices with improved performance and reliability.In addition to the semiconductor industry, fused silica substrates are also widely used in the production of optical components for telecommunications, laser systems, and high-powered optics. The exceptional optical transmission and thermal stability of fused silica make it an ideal material for these applications, and {} has been a strategic supplier of fused silica substrates to many companies in the optical industry. The company's commitment to quality and innovation has enabled it to gain the trust of its customers and establish itself as a leading supplier in this market.Furthermore, fused silica substrates have also found important applications in the aerospace and defense industries. The material's high thermal stability and low expansion coefficient make it suitable for use in harsh environmental conditions, such as those encountered in space and military applications. {} has been able to leverage its expertise in fused silica technology to develop substrates that meet the stringent requirements of these industries, providing reliable and high-performance solutions for critical applications.As the demand for high-quality fused silica substrates continues to grow across various industries, {} has consistently invested in research and development to further advance its manufacturing processes and product capabilities. The company's state-of-the-art production facilities and team of experienced engineers and scientists enable it to deliver customized solutions that meet the specific needs of its customers. This has allowed {} to maintain its position as a preferred supplier of fused silica substrates for many leading companies globally.In conclusion, the continued advancements in technology and the increasing demand for high-performance materials have made fused silica substrates an indispensable component in various industries. As a global leader in the development and production of advanced materials, {} has played a pivotal role in meeting this demand by delivering high-quality fused silica substrates that enable the production of cutting-edge electronic devices, optical components, and aerospace technologies. With its commitment to innovation and customer satisfaction, {} is well-positioned to continue driving the advancement of fused silica technology and providing reliable solutions for its customers' most demanding applications.
Durable and High-Quality Large Sapphire Windows for Various Applications
Large Sapphire Windows are creating a buzz in the tech industry with their groundbreaking technology and innovation. The company, a leader in the field of advanced sapphire products, has been making waves with their durable and high-quality sapphire windows that are revolutionizing various industries.As a leading provider of sapphire windows, they have been catering to the needs of a wide range of industries, including aerospace, defense, optics, and more. Their sapphire windows are known for their exceptional strength and durability, making them the perfect choice for applications that require high-performance optical components.The company’s sapphire windows are made from synthetic sapphire, which is created through a process called the Verneuil method. This method involves melting aluminum oxide and then slowly cooling it to create large, transparent sapphire crystals. These crystals are then cut and polished to create sapphire windows that are not only incredibly strong but also offer excellent optical clarity.One of the most significant advantages of Large Sapphire Windows' products is their exceptional hardness. The synthetic sapphire used in their windows is second only to diamond in terms of hardness, making it highly resistant to scratches and abrasion. This property makes sapphire windows an ideal choice for applications that require durable and long-lasting optical components.In addition to their impressive strength, Large Sapphire Windows' products also offer excellent optical properties. The high transparency and low distortion of sapphire windows make them the perfect choice for applications that require high-quality optical components, such as lenses and windows for imaging and sensing systems.The company's sapphire windows are also highly resistant to harsh environmental conditions, making them suitable for use in challenging environments. Whether it's extreme temperatures, corrosive chemicals, or high-pressure conditions, Large Sapphire Windows' products can withstand it all, making them a reliable choice for demanding applications.Large Sapphire Windows' commitment to innovation and quality has led to the development of a wide range of sapphire windows that cater to the diverse needs of their customers. Whether it's large windows for aerospace applications or small, precision windows for optical instruments, the company offers a variety of options to meet the specific requirements of different industries.The company's dedication to customer satisfaction is evident in their superior customer service and quick turnaround times. They understand the critical nature of their products in various applications, and they strive to deliver high-quality sapphire windows in a timely manner to ensure minimal downtime for their customers.With their innovative approach and commitment to excellence, Large Sapphire Windows has established itself as a reliable and trusted partner for companies looking for high-performance sapphire windows. Their products have set a new standard in the industry, and their continued dedication to research and development ensures that they will remain at the forefront of sapphire technology.In conclusion, Large Sapphire Windows has emerged as a leader in the field of sapphire windows, providing innovative and high-quality solutions to a wide range of industries. With their exceptional strength, durability, and optical properties, their products have redefined the possibilities for optical components, making them an invaluable asset for companies looking to push the boundaries of technology and innovation.
Discover the Latest Advancements in Crystal Substrate Technology
GSGG Crystal Substrate - a Cutting-Edge Material for Advanced TechnologyIn the world of advanced technology, the demand for high-performance materials has never been greater. One material that has been gaining attention in recent years is GSGG crystal substrate, which has shown great promise in various applications, from laser systems to optical devices. This cutting-edge material has the potential to revolutionize the way we approach advanced technology and is poised to become a critical component in the development of next-generation devices.GSGG crystal substrate is a type of crystal material that exhibits exceptional optical and physical properties, making it highly desirable for a wide range of applications. Its unique combination of high transparency, excellent thermal conductivity, and superior mechanical strength sets it apart from other materials currently available in the market. This makes GSGG crystal substrate an ideal choice for use in demanding environments where reliability and performance are paramount.One company that has been at the forefront of developing and manufacturing GSGG crystal substrates is {}. With a strong focus on research and development, {} has been able to produce high-quality GSGG crystal substrates that meet the stringent requirements of the most demanding applications. The company's state-of-the-art production facilities and advanced manufacturing techniques have enabled them to consistently deliver products that exceed industry standards and customer expectations.{}'s GSGG crystal substrates have found wide-ranging applications in various fields, including laser technology, telecommunications, aerospace, and medical devices. One of the key advantages of using GSGG crystal substrates in these applications is their exceptional thermal stability and optical clarity, which allows for high-power laser operation and precise optical transmission. This makes {}'s GSGG crystal substrates an ideal choice for demanding laser systems and optical devices where performance and reliability are non-negotiable.Furthermore, {}'s commitment to quality and innovation has positioned them as a leading supplier of GSGG crystal substrates in the global market. The company's dedicated team of experts continuously pushes the boundaries of material science and engineering to develop new and improved GSGG crystal substrates that address the evolving needs of the industry. As a result, {} has earned a reputation for being a trusted partner for organizations looking to incorporate GSGG crystal substrates into their advanced technology solutions.In addition to their extensive product line, {} also offers comprehensive technical support and customization services to its customers. This ensures that each GSGG crystal substrate meets the exact specifications and requirements of the application, allowing for seamless integration and optimal performance. {}'s dedication to customer satisfaction and their ability to provide tailored solutions further solidifies their position as a preferred supplier of GSGG crystal substrates in the market.Looking ahead, the future of GSGG crystal substrates looks promising, with continued advancements in material science and manufacturing techniques. As the demand for high-performance materials grows, GSGG crystal substrates are expected to play a pivotal role in enabling the next generation of advanced technology solutions. With {} at the helm, driving innovation and excellence in the development of GSGG crystal substrates, the industry can expect to see even greater potential unlocked in the years to come.In conclusion, GSGG crystal substrates have emerged as a game-changing material for advanced technology, with their exceptional optical and physical properties making them a preferred choice for a wide range of applications. As a leading manufacturer and supplier of GSGG crystal substrates, {} is well-positioned to meet the growing demand for these materials and drive further advancements in the industry. With their commitment to quality, innovation, and customer satisfaction, {} continues to be a driving force in the evolution of GSGG crystal substrates and their potential to shape the future of advanced technology.
Rare and Valuable Sapphire Ingot Discovered in Recent Excavation
Sapphire ingot, a key material widely used in various industries, is gaining attention in the market as its demand continues to rise.Sapphire ingots are high-purity, single-crystal forms of sapphire, a tough and transparent material that is second only to diamonds in terms of hardness. It is widely used in various industries, including electronics, aerospace, and medical equipment manufacturing. The material is known for its durability, scratch resistance, and high thermal conductivity, making it a popular choice for applications that require high-performance and reliability.One company that has been at the forefront of sapphire ingot production is . With a history of over 20 years in the industry, has established itself as a leading manufacturer of high-quality sapphire ingots. The company has a state-of-the-art production facility and a team of experienced engineers and researchers who are dedicated to continuously improving the quality and performance of their sapphire ingots.In addition to producing standard sapphire ingots, also offers customized solutions to meet the specific needs of their customers. They work closely with their clients to understand their requirements and provide tailored solutions that meet their exact specifications. This level of flexibility and customer-centric approach has earned a strong reputation in the industry and has helped them build long-term partnerships with their clients.The demand for sapphire ingots has been steadily increasing in recent years, driven by the growing adoption of sapphire-based products in various industries. In the electronics sector, sapphire ingots are used to produce substrates for LED and semiconductor applications. The material's superior thermal conductivity and high optical transparency make it an ideal choice for these applications. In the aerospace industry, sapphire ingots are used to create windows and dome covers for aircraft and spacecraft, thanks to their exceptional durability and resistance to high temperatures and pressure. Furthermore, sapphire ingots are also used in medical equipment manufacturing, where they are utilized in the production of high-performance optical components and surgical instruments.As the demand for sapphire ingots continues to grow, companies like are ramping up their production to meet the market's needs. With their commitment to quality and innovation, is well-positioned to capitalize on the increasing demand for sapphire ingots and maintain their leading position in the industry.To further strengthen their position in the market, is also investing in research and development to explore new applications and improve the performance of their sapphire ingots. They are collaborating with industry partners and academic institutions to drive innovation and develop cutting-edge solutions that push the boundaries of what sapphire ingots can achieve.In conclusion, the demand for sapphire ingots is on the rise, driven by their wide-ranging applications and superior performance characteristics. With their extensive experience, commitment to quality, and investment in R&D, companies like are well-equipped to meet the growing demand for sapphire ingots and continue to drive the industry forward. As the market for sapphire-based products continues to expand, the role of sapphire ingots will become even more prominent, making them a key material for the future of various industries.
High-quality Germanium Wafers for Semiconductor Applications
Germanium Wafer Market is anticipated to reach XX% CAGR during 2021-2026. Germanium is a lustrous, hard, grayish-white metalloid in the carbon group with an atomic number of 32 in the periodic table. Germanium wafer is used in various applications such as infrared optics, solar cells, nanowires, and others.The Germanium Wafer market is expected to witness significant growth due to the increasing demand for consumer electronics and the adoption of advanced technologies in the industry. The rise in demand for infrared optics and solar cells is also driving the growth of the Germanium wafer market. Additionally, the growing use of Germanium in the production of nanowires for semiconductors and optoelectronics is expected to further boost the market growth.The global Germanium Wafer market is segmented based on type, application, and region. Based on type, the market is divided into N-type, P-type, and others. N-type Germanium wafers are widely used in the production of solar cells and infrared optics, while P-type Germanium wafers find applications in nanowires and semiconductors.On the basis of application, the market is categorized into consumer electronics, solar cells, infrared optics, nanowires, and others. The consumer electronics segment is expected to dominate the market due to the increasing use of Germanium wafers in smartphones, tablets, and other electronic devices. The solar cells segment is also anticipated to witness significant growth due to the increasing demand for renewable energy sources.Regionally, the Germanium Wafer market is segmented into North America, Europe, Asia Pacific, Latin America, and Middle East & Africa. Asia Pacific is expected to dominate the market due to the presence of major consumer electronics manufacturers in the region. The increasing investments in the solar energy sector in countries like China and India are also driving the market growth in the region. Europe and North America are also expected to witness substantial growth due to the growing demand for advanced technologies in the region.{Company Name} is one of the leading manufacturers of Germanium wafers in the market. The company offers a wide range of Germanium wafers with superior quality and performance. {Company Name} has a strong presence in the global market and has a solid customer base in various industries.The company's Germanium wafers are widely used in the production of semiconductor devices, infrared optics, and solar cells. {Company Name} has a state-of-the-art manufacturing facility, equipped with advanced technologies to produce high-quality Germanium wafers that meet the industry standards and customer requirements.{Company Name} is known for its commitment to innovation and continuous improvement. The company invests heavily in research and development to develop advanced Germanium wafer technologies and enhance its product portfolio. {Company Name} also focuses on sustainability and environmental protection by adopting eco-friendly manufacturing processes and reducing its carbon footprint.The company has a strong distribution network and a dedicated sales team to cater to the growing demand for Germanium wafers in the global market. {Company Name} is committed to providing excellent customer service and technical support to its clients and partners.In conclusion, the global Germanium Wafer market is poised for significant growth in the coming years due to the increasing demand for consumer electronics, solar cells, and advanced technologies. {Company Name} is well-positioned to capitalize on this growth with its high-quality Germanium wafers and strong market presence. With its focus on innovation, sustainability, and customer satisfaction, {Company Name} is set to play a key role in shaping the future of the Germanium wafer market.
Solar Silicon Wafer Market Gains Momentum: A Promising Outlook for Growing Photovoltaic Industry
SolarTech Inc., a leading innovator in the solar energy industry, has recently announced the launch of their revolutionary Solar Silicon Wafer, a groundbreaking technology that promises to enhance the efficiency and reliability of solar panels. With this cutting-edge innovation, SolarTech aims to make a significant contribution to the global transition towards renewable energy sources.Solar energy has gained immense popularity in recent years as the world increasingly seeks sustainable alternatives to traditional sources of power. However, the efficiency of solar panels has been a persistent challenge in fully realizing the potential of this renewable energy source. SolarTech recognized this obstacle and set out to develop a solution that would revolutionize the solar industry.The newly introduced Solar Silicon Wafer is a game-changer in the solar energy sector. By combining advanced materials and state-of-the-art technology, SolarTech has created a high-performance silicon wafer that boasts unparalleled efficiency and durability. This breakthrough innovation not only maximizes the conversion of sunlight into electricity but also ensures the longevity of solar panels, making them a more reliable and cost-effective solution.The key to the superior performance of SolarTech's Solar Silicon Wafer lies in its unique composition and manufacturing process. The company employs a proprietary technique that allows them to produce silicon wafers with enhanced crystal structures, resulting in higher conversion rates and improved overall efficiency. Furthermore, SolarTech utilizes a combination of anti-reflective coatings and passivation layers to minimize energy loss and increase the durability of the wafer.One of the standout features of SolarTech's Solar Silicon Wafer is its ability to capture a broader spectrum of light, including both visible and infrared wavelengths. Traditional solar panels often struggle to harness infrared light, leading to a significant loss of potential energy. By overcoming this limitation, SolarTech's wafer can generate more electricity from the same amount of sunlight, significantly increasing the overall efficiency of solar panels.Another advantage offered by SolarTech's Solar Silicon Wafer is its strength and resilience. The company employs innovative manufacturing techniques that result in a highly durable wafer, capable of withstanding extreme weather conditions and harsh environments. This durability ensures that solar panels utilizing SolarTech's wafer are longer-lasting, providing a more sustainable and cost-effective solution for consumers and businesses alike.SolarTech's commitment to sustainability extends beyond their groundbreaking product. The company is dedicated to minimizing its environmental impact throughout the manufacturing and distribution processes. SolarTech has implemented several initiatives to reduce waste generation, optimize energy consumption, and lower greenhouse gas emissions. By prioritizing sustainability, SolarTech aims to lead by example and inspire others in the solar industry to adopt eco-friendly practices.The introduction of SolarTech's Solar Silicon Wafer has garnered significant attention from industry experts and consumers alike. The groundbreaking technology holds the potential to drive the mass adoption of solar energy by addressing the efficiency and reliability concerns that have hindered its progress. As countries continue to make ambitious commitments towards reducing greenhouse gas emissions and combating climate change, SolarTech's advanced silicon wafer could play a pivotal role in harnessing the power of the sun on a global scale.In conclusion, SolarTech Inc. has unveiled their revolutionary Solar Silicon Wafer, a groundbreaking technology that promises to revolutionize the solar energy industry. With its unmatched efficiency, durability, and ability to capture a broader spectrum of light, SolarTech's wafer sets a new standard for solar panel performance. The company's commitment to sustainability further solidifies their position as a leading innovator in the renewable energy sector. As the world strives towards a greener future, SolarTech's Solar Silicon Wafer offers a promising solution that could propel the adoption of solar energy to unprecedented heights.
Discover the Latest Advancements in Wafer Window Technology
Mgo Wafer Windows Revolutionize the Window Industry[Company Name], a leading innovative materials technology company, has recently introduced a revolutionary product that is set to transform the window industry. Mgo Wafer Windows, a groundbreaking development in window technology, promise increased durability, enhanced thermal insulation, and improved soundproofing. With their innovative design and advanced properties, these windows are poised to become the go-to choice for architects, builders, and homeowners alike.Traditional windows have long been plagued by issues such as susceptibility to damage, limited insulation capabilities, and poor soundproofing. [Company Name] recognized these pain points and embarked on a mission to develop a solution that would alleviate these problems. The result of their relentless research and development efforts is the Mgo Wafer Windows – a product that promises to revolutionize the way we think about and experience windows.One of the key advantages of Mgo Wafer Windows is their exceptional durability. Unlike traditional windows, which are prone to cracks, discoloration, and warping over time, Mgo Wafer Windows are composed of magnesium oxide, a material known for its high strength and resistance to wear and tear. This superior durability ensures that the windows retain their aesthetic appeal and functionality for extended periods, saving homeowners from the hassle and cost of regular replacements.Furthermore, Mgo Wafer Windows excel in thermal insulation, offering a significant improvement over conventional windows. These windows feature advanced insulation properties that minimize heat transfer, resulting in reduced energy consumption for heating or cooling buildings. As a result, homeowners can enjoy a more comfortable and energy-efficient living environment while simultaneously reducing their carbon footprint.Another area where Mgo Wafer Windows shine is soundproofing. The advanced design of these windows incorporates multiple layers of sound-dampening materials, effectively reducing noise pollution from outside sources. This is particularly beneficial for urban areas, where excessive noise can negatively impact the quality of life. Mgo Wafer Windows provide the peace and tranquility that homeowners desire, allowing them to relax and unwind without disturbances.Additionally, Mgo Wafer Windows offer an array of customizable options, ensuring they seamlessly blend with various architectural styles. Homeowners and architects can choose from a wide range of sizes, shapes, and designs to meet their unique preferences and requirements. This versatility allows for creativity in design and enhances the overall aesthetics of any building or space.In terms of installation and maintenance, Mgo Wafer Windows provide added convenience. The lightweight nature of magnesium oxide makes these windows easy to handle and install, saving time and effort during the construction process. Moreover, the low maintenance requirements of Mgo Wafer Windows help homeowners avoid constant upkeep and reduce long-term costs associated with repairs.With the introduction of Mgo Wafer Windows, [Company Name] has disrupted the traditional window industry and set new standards for excellence. These windows promise remarkable durability, energy efficiency, enhanced soundproofing, and aesthetic versatility – a combination of features that makes them an ideal choice for both residential and commercial buildings.As the demand for sustainable and efficient building materials continues to grow, Mgo Wafer Windows position [Company Name] at the forefront of innovation in the window industry. With a commitment to excellence and a focus on customer satisfaction, [Company Name] is poised to lead the charge in transforming the way we view and experience windows. The advent of Mgo Wafer Windows marks a crucial milestone in the progression of architecture and construction, and it is only a matter of time before these windows become the new industry standard.
Top Silicon Carbide Polishing Product for Optimal Shine
Silicon Carbide Polishing: The Key to Achieving Unmatched PrecisionIn today's fast-paced and competitive world, industries are constantly seeking new and innovative ways to improve the quality and precision of their products. Whether in the field of electronics, automotive, aerospace, or any other industry, achieving the highest level of precision is crucial for maintaining a competitive edge. One company that has been leading the way in this regard is {}.{} is a renowned leader in providing state-of-the-art solutions for precision polishing, and one of their key offerings is their innovative Silicon Carbide Polishing technology. This cutting-edge technology has revolutionized the way industries achieve precision polishing, making it possible to reach unmatched levels of quality and performance.Silicon Carbide Polishing is a process that involves the use of abrasive silicon carbide particles to remove material and create a smooth and polished surface. This technology is widely utilized in a variety of industries, including semiconductor manufacturing, optical components production, and precision engineering. Silicon Carbide Polishing offers numerous advantages over traditional polishing methods, including higher precision, improved efficiency, and enhanced surface finish.One of the key factors that sets {}'s Silicon Carbide Polishing technology apart from the competition is the company's dedication to research and development. With a team of highly skilled engineers and researchers, {} continuously strives to improve and innovate their polishing technology, ensuring that their customers are always at the forefront of precision polishing capabilities.The use of Silicon Carbide Polishing has become increasingly prevalent in the semiconductor industry, where the demand for ultra-precise and defect-free surfaces is paramount. With {}'s Silicon Carbide Polishing technology, semiconductor manufacturers can achieve the high level of flatness and smoothness required for their products, leading to increased yields and improved overall quality.In the field of optical components production, Silicon Carbide Polishing has also proven to be a game-changer. By utilizing {}'s cutting-edge technology, manufacturers can achieve superior surface quality and precision, which is essential for the production of high-quality lenses, mirrors, and other optical components.{}'s Silicon Carbide Polishing technology has also found widespread application in the precision engineering industry, where the need for ultra-precise and smooth surfaces is crucial. By using Silicon Carbide Polishing, manufacturers can achieve the level of precision required for critical components such as gears, bearings, and shafts, leading to improved performance and longevity of the final products.In addition to their innovative Silicon Carbide Polishing technology, {} is also known for their exceptional customer service and support. With a strong focus on understanding their customers' unique requirements, {} offers customized solutions to cater to the specific needs of each industry and application. This customer-centric approach has earned {} a reputation as a trusted partner in the precision polishing industry.Furthermore, {}'s commitment to sustainability is evident in their Silicon Carbide Polishing technology, with a focus on minimizing waste and energy consumption. By optimizing the polishing process, {} helps their customers reduce their environmental footprint while still achieving the highest level of precision and quality.With the increasing demand for high-precision products across various industries, the importance of Silicon Carbide Polishing technology provided by {} cannot be overstated. As industries continue to push the boundaries of precision and performance, {} remains at the forefront of innovation, providing cutting-edge solutions that empower their customers to achieve unmatched levels of quality and precision in their products.
Understanding Fused Silica Wafer and Its Applications in the Electronics Industry
Title: Fused Silica Wafer: Leading the Semiconductor Industry with Enhanced Efficiency and PrecisionIntroduction:Fused Silica wafer (Brand name removed), a prominent player in the semiconductor industry, has gained recognition for its cutting-edge technology and unparalleled quality. With a strong commitment to research and development, the company has revolutionized the fabrication process of semiconductor devices by introducing high-quality fused silica wafers. These wafers are designed to enhance efficiency and precision, catering to the evolving needs of the electronics industry. By consistently delivering innovative solutions, (Company name) has positioned itself as a leader in the market.Enhancing Efficiency:Fused Silica wafers are specifically engineered to boost the efficiency of semiconductor device manufacturing. These wafers possess exceptional thermal stability, low thermal expansion coefficients, and excellent resistance to high temperatures. These properties allow them to withstand demanding manufacturing processes without compromising the overall performance of the semiconductor devices. As a result, manufacturers utilizing Fused Silica wafers can streamline their production, eliminate defects, and ensure a higher yield, delivering cost-effective solutions to customers.Ensuring Precision:Precision is vital in semiconductor device manufacturing, and Fused Silica wafers excel in providing the necessary accuracy and uniformity. The superior surface quality and high crystal orientation uniformity of these wafers enable the precise integration of various microelectronic components. Moreover, the wafers exhibit an extremely low defect density, resulting in reduced signal attenuation and superior electrical properties. This level of precision offered by Fused Silica wafers ensures the creation of reliable and high-performance semiconductor devices.Advanced Technology:One of the primary reasons behind the success of Fused Silica wafer lies in its commitment to leveraging advanced technologies. (Company name) boasts state-of-the-art facilities equipped with cutting-edge manufacturing techniques, including chemical vapor deposition and advanced polishing technologies. These technologies allow the company to produce wafers with exceptional surface quality and crystalline uniformity, meeting the stringent requirements of the semiconductor industry. By continuously investing in research and development, (Company name) stays at the forefront of innovation, offering customers the most advanced fused silica wafers available.Market Impact:The introduction of Fused Silica wafers has significantly impacted the semiconductor industry by addressing the growing demand for efficient and precise manufacturing solutions. By collaborating with major semiconductor manufacturing companies, (Company name) has established itself as a trusted partner in delivering high-quality wafers. These partnerships have facilitated the development of customized solutions, tailored to meet the specific requirements of different applications, such as microelectronics, optical devices, and nanotechnology. As a result, Fused Silica wafers have gained widespread adoption, contributing to the overall growth and scalability of the semiconductor market.Future Outlook:Looking ahead, Fused Silica wafers are expected to continue driving innovation in the semiconductor industry. With ongoing research, the company aims to further enhance key properties of the wafers, such as thermal stability and crystal uniformity, to cater to emerging technologies like Internet of Things (IoT) devices, artificial intelligence, and autonomous vehicles. By collaborating with industry leaders, (Company name) remains committed to revolutionizing semiconductor fabrication, enabling the development of next-generation electronic devices that will shape our future.Conclusion:Fused Silica wafer (Brand name removed) has become synonymous with excellence and innovation in the semiconductor industry. Its commitment to delivering efficient and precise solutions has positioned the company as a trusted partner for major semiconductor manufacturers. Through advanced technology and continuous research and development, (Company name) ensures the production of high-quality fused silica wafers, driving the growth and advancement of the industry. With a promising future ahead, (Company name) is poised to revolutionize semiconductor fabrication and contribute to the next wave of technological advancements.
Highly Durable Ceramic Material Zirconia Oxide Gains Attention in Various Industries
Zro2 Ceramic Material Revolutionizing the IndustryZro2 Ceramic Material, a cutting-edge innovation in the world of ceramics, is currently taking the industry by storm. This revolutionary material is changing the game with its superior strength, durability, and resistance to extreme temperatures. With a wide range of applications across various industries, Zro2 Ceramic Material is proving to be a game-changer in the world of advanced ceramics.The company behind this groundbreaking material, has been at the forefront of innovation and research in the field of ceramics for decades. Their team of expert engineers and scientists have developed a proprietary process for creating Zro2 Ceramic Material that sets it apart from traditional ceramics. By combining zirconia and other advanced materials, they have been able to produce a material that exhibits exceptional physical and mechanical properties.One of the key advantages of Zro2 Ceramic Material is its outstanding strength and durability. With a hardness level that rivals that of diamonds, this material is incredibly resistant to wear and abrasion. This makes it ideal for use in various industrial applications, such as cutting tools, ball bearings, and wear-resistant components. In addition, its high flexural strength and fracture toughness make it perfect for use in high-stress environments.Furthermore, Zro2 Ceramic Material boasts remarkable resistance to extreme temperatures, making it suitable for use in environments where traditional ceramics would fail. Its ability to withstand high temperatures without compromising its structural integrity makes it an ideal choice for applications in the aerospace, automotive, and energy industries. In addition, this material is highly corrosion-resistant, making it a popular choice for use in chemical processing and marine applications.The versatility of Zro2 Ceramic Material is another factor that sets it apart from traditional ceramics. Its ability to be formed into complex shapes and sizes, coupled with its superior performance, makes it a preferred choice for a wide range of applications. From medical instruments to thermal barrier coatings, this material offers solutions to challenges that were previously unattainable with traditional ceramics.Moreover, the company's commitment to sustainability is reflected in the production of Zro2 Ceramic Material. By utilizing advanced manufacturing techniques and eco-friendly processes, they have been able to minimize waste and energy consumption while producing this state-of-the-art material. This dedication to environmental responsibility sets them apart as a leader in the industry.The impact of Zro2 Ceramic Material is being felt across various industries, with manufacturers and engineers recognizing its potential to elevate their products and processes. As demands for high-performance materials continue to rise, this innovative material is poised to play a pivotal role in shaping the future of advanced ceramics.In conclusion, Zro2 Ceramic Material has emerged as a game-changer in the world of ceramics, offering unrivaled strength, durability, and resistance to extreme temperatures. With a wide range of applications across diverse industries, this revolutionary material is poised to drive innovation and advancements in the field of advanced ceramics. As the company continues to push the boundaries of material science and engineering, the impact of Zro2 Ceramic Material is set to be felt for years to come.
Durable Fused Silica Substrate Technology: What You Need to Know
Fused Silica Substrate is a critical component in the manufacturing of various high-tech products, and one company leading the way in producing this essential material is {}. {} is a global leader in the development and production of advanced materials and solutions for a wide range of industries, including electronics, telecommunications, and aerospace. The company has a proven track record of delivering high-quality products and has established itself as a trusted partner for many leading companies around the world.Fused silica is a type of glass that is made from high-purity silica sand, which is melted and then solidified to form a transparent and highly durable material. It is known for its excellent thermal stability, low thermal expansion, and high optical transmission, making it an ideal substrate for a variety of applications. {} has developed advanced manufacturing processes to produce fused silica substrates with precise dimensions and superior optical and mechanical properties, meeting the stringent requirements of its customers.One of the key applications of fused silica substrates is in the production of semiconductor devices. As the semiconductor industry continues to advance, there is a growing demand for high-quality substrates that can meet the increasing performance and reliability requirements of advanced electronic devices. {} has been at the forefront of meeting this demand by developing fused silica substrates that enable the production of cutting-edge semiconductor devices with improved performance and reliability.In addition to the semiconductor industry, fused silica substrates are also widely used in the production of optical components for telecommunications, laser systems, and high-powered optics. The exceptional optical transmission and thermal stability of fused silica make it an ideal material for these applications, and {} has been a strategic supplier of fused silica substrates to many companies in the optical industry. The company's commitment to quality and innovation has enabled it to gain the trust of its customers and establish itself as a leading supplier in this market.Furthermore, fused silica substrates have also found important applications in the aerospace and defense industries. The material's high thermal stability and low expansion coefficient make it suitable for use in harsh environmental conditions, such as those encountered in space and military applications. {} has been able to leverage its expertise in fused silica technology to develop substrates that meet the stringent requirements of these industries, providing reliable and high-performance solutions for critical applications.As the demand for high-quality fused silica substrates continues to grow across various industries, {} has consistently invested in research and development to further advance its manufacturing processes and product capabilities. The company's state-of-the-art production facilities and team of experienced engineers and scientists enable it to deliver customized solutions that meet the specific needs of its customers. This has allowed {} to maintain its position as a preferred supplier of fused silica substrates for many leading companies globally.In conclusion, the continued advancements in technology and the increasing demand for high-performance materials have made fused silica substrates an indispensable component in various industries. As a global leader in the development and production of advanced materials, {} has played a pivotal role in meeting this demand by delivering high-quality fused silica substrates that enable the production of cutting-edge electronic devices, optical components, and aerospace technologies. With its commitment to innovation and customer satisfaction, {} is well-positioned to continue driving the advancement of fused silica technology and providing reliable solutions for its customers' most demanding applications.
Durable and High-Quality Large Sapphire Windows for Various Applications
Large Sapphire Windows are creating a buzz in the tech industry with their groundbreaking technology and innovation. The company, a leader in the field of advanced sapphire products, has been making waves with their durable and high-quality sapphire windows that are revolutionizing various industries.As a leading provider of sapphire windows, they have been catering to the needs of a wide range of industries, including aerospace, defense, optics, and more. Their sapphire windows are known for their exceptional strength and durability, making them the perfect choice for applications that require high-performance optical components.The company’s sapphire windows are made from synthetic sapphire, which is created through a process called the Verneuil method. This method involves melting aluminum oxide and then slowly cooling it to create large, transparent sapphire crystals. These crystals are then cut and polished to create sapphire windows that are not only incredibly strong but also offer excellent optical clarity.One of the most significant advantages of Large Sapphire Windows' products is their exceptional hardness. The synthetic sapphire used in their windows is second only to diamond in terms of hardness, making it highly resistant to scratches and abrasion. This property makes sapphire windows an ideal choice for applications that require durable and long-lasting optical components.In addition to their impressive strength, Large Sapphire Windows' products also offer excellent optical properties. The high transparency and low distortion of sapphire windows make them the perfect choice for applications that require high-quality optical components, such as lenses and windows for imaging and sensing systems.The company's sapphire windows are also highly resistant to harsh environmental conditions, making them suitable for use in challenging environments. Whether it's extreme temperatures, corrosive chemicals, or high-pressure conditions, Large Sapphire Windows' products can withstand it all, making them a reliable choice for demanding applications.Large Sapphire Windows' commitment to innovation and quality has led to the development of a wide range of sapphire windows that cater to the diverse needs of their customers. Whether it's large windows for aerospace applications or small, precision windows for optical instruments, the company offers a variety of options to meet the specific requirements of different industries.The company's dedication to customer satisfaction is evident in their superior customer service and quick turnaround times. They understand the critical nature of their products in various applications, and they strive to deliver high-quality sapphire windows in a timely manner to ensure minimal downtime for their customers.With their innovative approach and commitment to excellence, Large Sapphire Windows has established itself as a reliable and trusted partner for companies looking for high-performance sapphire windows. Their products have set a new standard in the industry, and their continued dedication to research and development ensures that they will remain at the forefront of sapphire technology.In conclusion, Large Sapphire Windows has emerged as a leader in the field of sapphire windows, providing innovative and high-quality solutions to a wide range of industries. With their exceptional strength, durability, and optical properties, their products have redefined the possibilities for optical components, making them an invaluable asset for companies looking to push the boundaries of technology and innovation.
Discover the Latest Advancements in Crystal Substrate Technology
GSGG Crystal Substrate - a Cutting-Edge Material for Advanced TechnologyIn the world of advanced technology, the demand for high-performance materials has never been greater. One material that has been gaining attention in recent years is GSGG crystal substrate, which has shown great promise in various applications, from laser systems to optical devices. This cutting-edge material has the potential to revolutionize the way we approach advanced technology and is poised to become a critical component in the development of next-generation devices.GSGG crystal substrate is a type of crystal material that exhibits exceptional optical and physical properties, making it highly desirable for a wide range of applications. Its unique combination of high transparency, excellent thermal conductivity, and superior mechanical strength sets it apart from other materials currently available in the market. This makes GSGG crystal substrate an ideal choice for use in demanding environments where reliability and performance are paramount.One company that has been at the forefront of developing and manufacturing GSGG crystal substrates is {}. With a strong focus on research and development, {} has been able to produce high-quality GSGG crystal substrates that meet the stringent requirements of the most demanding applications. The company's state-of-the-art production facilities and advanced manufacturing techniques have enabled them to consistently deliver products that exceed industry standards and customer expectations.{}'s GSGG crystal substrates have found wide-ranging applications in various fields, including laser technology, telecommunications, aerospace, and medical devices. One of the key advantages of using GSGG crystal substrates in these applications is their exceptional thermal stability and optical clarity, which allows for high-power laser operation and precise optical transmission. This makes {}'s GSGG crystal substrates an ideal choice for demanding laser systems and optical devices where performance and reliability are non-negotiable.Furthermore, {}'s commitment to quality and innovation has positioned them as a leading supplier of GSGG crystal substrates in the global market. The company's dedicated team of experts continuously pushes the boundaries of material science and engineering to develop new and improved GSGG crystal substrates that address the evolving needs of the industry. As a result, {} has earned a reputation for being a trusted partner for organizations looking to incorporate GSGG crystal substrates into their advanced technology solutions.In addition to their extensive product line, {} also offers comprehensive technical support and customization services to its customers. This ensures that each GSGG crystal substrate meets the exact specifications and requirements of the application, allowing for seamless integration and optimal performance. {}'s dedication to customer satisfaction and their ability to provide tailored solutions further solidifies their position as a preferred supplier of GSGG crystal substrates in the market.Looking ahead, the future of GSGG crystal substrates looks promising, with continued advancements in material science and manufacturing techniques. As the demand for high-performance materials grows, GSGG crystal substrates are expected to play a pivotal role in enabling the next generation of advanced technology solutions. With {} at the helm, driving innovation and excellence in the development of GSGG crystal substrates, the industry can expect to see even greater potential unlocked in the years to come.In conclusion, GSGG crystal substrates have emerged as a game-changing material for advanced technology, with their exceptional optical and physical properties making them a preferred choice for a wide range of applications. As a leading manufacturer and supplier of GSGG crystal substrates, {} is well-positioned to meet the growing demand for these materials and drive further advancements in the industry. With their commitment to quality, innovation, and customer satisfaction, {} continues to be a driving force in the evolution of GSGG crystal substrates and their potential to shape the future of advanced technology.
Rare and Valuable Sapphire Ingot Discovered in Recent Excavation
Sapphire ingot, a key material widely used in various industries, is gaining attention in the market as its demand continues to rise.Sapphire ingots are high-purity, single-crystal forms of sapphire, a tough and transparent material that is second only to diamonds in terms of hardness. It is widely used in various industries, including electronics, aerospace, and medical equipment manufacturing. The material is known for its durability, scratch resistance, and high thermal conductivity, making it a popular choice for applications that require high-performance and reliability.One company that has been at the forefront of sapphire ingot production is . With a history of over 20 years in the industry, has established itself as a leading manufacturer of high-quality sapphire ingots. The company has a state-of-the-art production facility and a team of experienced engineers and researchers who are dedicated to continuously improving the quality and performance of their sapphire ingots.In addition to producing standard sapphire ingots, also offers customized solutions to meet the specific needs of their customers. They work closely with their clients to understand their requirements and provide tailored solutions that meet their exact specifications. This level of flexibility and customer-centric approach has earned a strong reputation in the industry and has helped them build long-term partnerships with their clients.The demand for sapphire ingots has been steadily increasing in recent years, driven by the growing adoption of sapphire-based products in various industries. In the electronics sector, sapphire ingots are used to produce substrates for LED and semiconductor applications. The material's superior thermal conductivity and high optical transparency make it an ideal choice for these applications. In the aerospace industry, sapphire ingots are used to create windows and dome covers for aircraft and spacecraft, thanks to their exceptional durability and resistance to high temperatures and pressure. Furthermore, sapphire ingots are also used in medical equipment manufacturing, where they are utilized in the production of high-performance optical components and surgical instruments.As the demand for sapphire ingots continues to grow, companies like are ramping up their production to meet the market's needs. With their commitment to quality and innovation, is well-positioned to capitalize on the increasing demand for sapphire ingots and maintain their leading position in the industry.To further strengthen their position in the market, is also investing in research and development to explore new applications and improve the performance of their sapphire ingots. They are collaborating with industry partners and academic institutions to drive innovation and develop cutting-edge solutions that push the boundaries of what sapphire ingots can achieve.In conclusion, the demand for sapphire ingots is on the rise, driven by their wide-ranging applications and superior performance characteristics. With their extensive experience, commitment to quality, and investment in R&D, companies like are well-equipped to meet the growing demand for sapphire ingots and continue to drive the industry forward. As the market for sapphire-based products continues to expand, the role of sapphire ingots will become even more prominent, making them a key material for the future of various industries.