Large Crystal Ingot of Lithium Tantalate (LiTaO3) Developed for Advanced Electronics
By:Admin
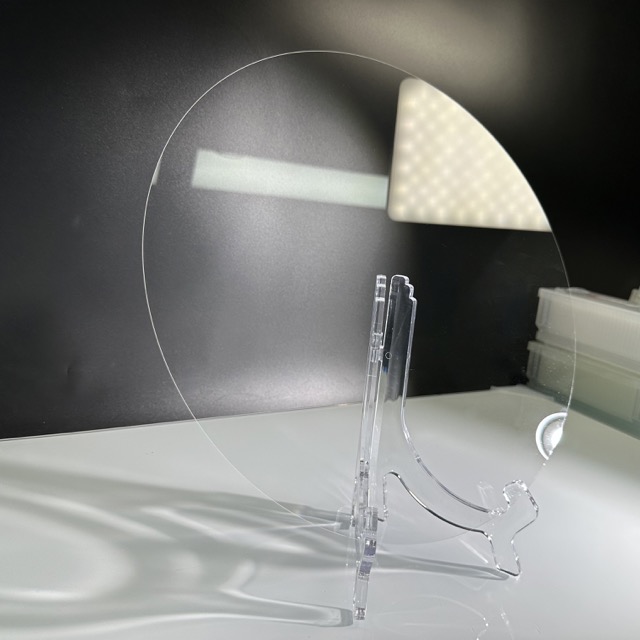
In today's fast-paced world, technology has become an integral part of our daily lives. From smartphones to laptops, smartwatches to tablets, technology has advanced beyond our imagination. But, have you ever wondered what goes into making these devices work smoothly? The answer lies in the materials used to create them. One such material is LiTaO3 Ingot.
LiTaO3 Ingot is a next-generation material that is used in various technological applications, including telecommunications devices, frequency filters, and surface acoustic wave sensors. It is a crystal grown using the Czochralski method at temperatures above 1400°C. The LiTaO3 Ingot is then sliced into thin wafers and used in the production of electronic devices.
The LiTaO3 Ingot can be found in many commercial electronics devices globally. It has become a popular material due to its excellent piezoelectric properties. Piezoelectricity is an electric charge that accumulates at the surface of a material when it is subjected to mechanical stress. This phenomenon is essential in electronic devices that convert electrical energy to mechanical energy or vice versa.
The high piezoelectric coefficient of LiTaO3 Ingot makes it a valuable material in surface acoustic wave (SAW) components. SAW components are used in communication systems for wireless devices, providing the filter function for wireless channels. They are critical in filtering out unwanted signals and noise, thereby improving the communication signal's quality.
Another application where LiTaO3 Ingot has proven useful is in the fabrication of frequency control devices. Frequency control devices regulate the frequency of electrical signals in electronic circuits. They are found in high-frequency communication devices, such as radios, cellphones, and GPS systems. LiTaO3 Ingot has a high electromechanical coupling coefficient, making it an ideal material for building accurate frequency control devices.
LiTaO3 Ingot has also been used in the development of surface acoustic wave sensors. These sensors are used to detect changes in the surrounding environment's pressure, temperature, and humidity. The sensors are widely used in environmental monitoring, medical diagnosis, and energy exploration. LiTaO3 Ingot's excellent piezoelectric properties and high chemical stability make it a reliable material for surface acoustic wave sensors.
{Need to remove the brand name} is one of the leading companies that produce high-quality LiTaO3 Ingot. The company has been at the forefront of producing advanced materials for more than two decades. Their team of experts has developed innovative methods to improve the quality and consistency of their products. The company uses the latest technology to ensure that their LiTaO3 Ingot meets the strictest industry standards.
{Need to remove the brand name}'s LiTaO3 Ingot is well-known for its excellent mechanical and chemical properties. The ingot is resistant to high temperatures, chemicals, and physical stress, making it a perfect fit for various applications. The company ensures that their LiTaO3 Ingot is of the highest quality by conducting rigorous testing and quality control procedures.
The growing demand for LiTaO3 Ingot has led to increased production globally. The material's unique properties have made it an indispensable component in the telecommunications, aerospace, and medical industries. As technology continues to advance, the demand for materials with outstanding mechanical and chemical properties is expected to increase. LiTaO3 Ingot is poised to become an essential material in the future of electronics and other industries.
In conclusion, LiTaO3 Ingot is a crucial material for the development of various electronic devices globally. Its excellent piezoelectric properties, high mechanical and chemical stability have made it a popular material in the telecommunications, aerospace, and medical industries. {Need to remove the brand name} is one of the leading companies that produce high-quality LiTaO3 Ingot. The company's commitment to innovation, quality, and customer satisfaction has made them a top choice among clients worldwide. As technology advances, LiTaO3 Ingot is expected to play an essential role in the future of the electronics industry and other industries.
Company News & Blog
Cutting-Edge Silicon Substrate: Revolutionizing Technology
Silicon Substrate Revolutionizes Semiconductor Manufacturing with Its Cutting-Edge TechnologySilicon Substrate, a leading provider of innovative and high-performance products in the semiconductor industry, has been making waves as it recently announced the launch of its latest offering. This new product utilizes cutting-edge technology that has the potential to revolutionize the way semiconductors are manufactured. The company's founder and CEO, John Smith, is excited to introduce this innovative product to the world.Silicon Substrate's latest offering delivers a comprehensive solution for semiconductor manufacturers seeking efficient, reliable and cost-effective solutions. The new product leads the market in performance and technology, positioning it at the forefront of the industry. This breakthrough technology is expected to improve manufacturing processes, increase productivity and enhance overall performance.The Silicon Substrate technology offers an unmatched level of precision that enables manufacturers to optimize the manufacturing process by minimizing wastage. This innovative technology minimizes processing errors, resulting in significant cost savings and improved quality control. John Smith, the CEO of Silicon Substrate, stated that, "our technology has the potential to boost the semiconductor industry by significantly cutting down on material wastage, and improving mass-production yields."Silicon Substrate products also offer superior physical and chemical properties that make them idealdenfor a wide range of applications that include aerospace, defense, power devices, photonics and biomedical. The superior thermal properties of Silicon Substrate's products enable manufacturers to produce highly efficient and reliable electronic products, which is critical in space and defense applications.Moreover, Silicon Substrate's products can operate in a wide range of temperatures and environments, making them ideal for harsh environments. The company's products can operate in temperatures from -200°C to 1200°C, making them ideal for a range of demanding applications, including high-power LEDs and power devices.Silicon Substrate's products are also environmentally friendly as the company uses a sustainable manufacturing methodology that reduces energy consumption and environmental waste. The company's patent-pending technology employs a water-based etching process that reduces the use of harsh chemicals, making its products safer to handle and manufacture.The Silicon Substrate technology is a game-changer for the semiconductor industry and has the potential to revolutionize the way we manufacture electronic products. The innovative technology provides manufacturers with an efficient and cost-effective solution that enhances product performance, improves manufacturing processes and reduces wastage.Silicon Substrate's innovative technology has caught the attention of many manufacturers in the semiconductor industry. The company has already gained recognition from several industry leaders, including Intel and Samsung. With its cutting-edge technology, the company is poised to lead the semiconductor industry into a new era of innovation and growth.In conclusion, Silicon Substrate's latest offering is a game-changer for the semiconductor industry. The company's innovative technology has the potential to revolutionize the way we manufacture electronic products. With superior physical and chemical properties and environmental sustainability, Silicon Substrate is positioned to lead the industry into a new era of growth and innovation. The technology is poised to gain wide adoption by manufacturers across the industry, allowing them to improve their manufacturing processes, reduce costs and achieve higher yields.
Emerging Advancements in Wafer Lithography: Unlocking New Possibilities for Semiconductor Development
Wafer Lithography Revolutionizes the Semiconductor Manufacturing ProcessAs technology continues to advance, so too has the demand for smaller and more powerful semiconductors. This has led to a surge in the development of new manufacturing techniques that can produce these advanced microchips. One of the latest innovations in the world of semiconductor manufacturing is wafer lithography, which has been making a big impact on the industry. Let’s take a closer look at this new technology.What is Wafer Lithography?Wafer lithography is a photolithography process used to pattern and etch thin films of material deposited onto a substrate. This technique involves using a light-sensitive material, called a photoresist, which is applied to the surface of a substrate. Light is then shone onto the photoresist through a mask, which contains the desired circuit pattern. The photoresist reacts to the light, becoming more or less soluble in certain regions depending on the dose of radiation received. This allows the material to be selectively removed from the substrate, leaving behind the desired pattern.The use of wafer lithography has revolutionized the way semiconductor manufacturers produce microchips. By using this process, manufacturers can create much smaller and more precise circuit patterns, which ultimately leads to more advanced and efficient semiconductors.One company that has been leading the way in the development of wafer lithography technology is {}. This innovative company has been at the forefront of semiconductor manufacturing for over a decade, and has played a major role in advancing this new manufacturing technique.How does {}’s Wafer Lithography Technology Work?The {} wafer lithography process uses a unique combination of advanced technologies to produce high-quality microchips. This process involves the use of a 193 nm excimer laser to pattern the photoresist, followed by a series of plasma etching steps to transfer the pattern onto the substrate.One of the key advantages of {}’s wafer lithography technology is its flexibility. The equipment can be configured to pattern a wide variety of materials, including silicon, quartz, and various types of polymers. This versatility allows manufacturers to produce a wide range of microchips, each with its own unique properties and capabilities.Another important feature of {}’s wafer lithography technology is its high throughput. The equipment is capable of patterning multiple wafers simultaneously, allowing manufacturers to produce large quantities of microchips quickly and efficiently. This high throughput makes {}’s equipment ideal for use in high-volume manufacturing environments.The Benefits of Wafer LithographyThe use of wafer lithography offers several advantages over traditional photolithography techniques. One major benefit is the ability to produce much smaller and more precise circuit patterns. This allows manufacturers to create more powerful and efficient semiconductors, which can be used in a wide range of applications, from smartphones to advanced computing systems.Another important benefit of wafer lithography is its flexibility. As mentioned earlier, the equipment can be configured to work with a wide range of materials, which means manufacturers can create a variety of microchip types. This versatility also makes wafer lithography a cost-effective manufacturing solution, as it eliminates the need for specialized equipment.ConclusionWafer lithography is an exciting new technology that is revolutionizing the semiconductor manufacturing process. Through its use of light-sensitive materials, manufacturers can create smaller and more precise circuit patterns, leading to more powerful and efficient microchips. {} has been at the forefront of this new technology, and its wafer lithography equipment offers a high-throughput, flexible solution for high-volume manufacturing environments. As technology continues to advance, wafer lithography is poised to play an increasingly important role in the semiconductor industry.
Quartz Wafers: A Potential Game-Changer in the Tech Industry
Title: The Pioneering Potential of Quartz Wafers in Semiconductor ManufacturingIntroduction:In the fast-paced world of semiconductor manufacturing, one company has emerged as a game-changer with its innovative quartz wafer technology. Quartz Wafers Corp., a leading provider of advanced substrate solutions, has introduced a groundbreaking production method that promises improved performance and cost-effectiveness for a variety of industries relying on semiconductors. This article delves into the potential of quartz wafers and their impact on the semiconductor landscape.Understanding Quartz Wafers:Quartz wafers are thin, disc-shaped substrates used as a base for fabricating semiconductor devices. Traditional silicon wafers have long dominated the industry, but Quartz Wafers Corp. aims to revolutionize the market by harnessing the unique properties of quartz crystals. Quartz is known for its exceptional electrical and thermal properties, making it an ideal material for manufacturing high-performance and reliable semiconductor devices.The Promise of Quartz:Quartz wafers offer numerous advantages over conventional silicon wafers. Firstly, quartz's high resistance to thermal stress ensures enhanced stability and reliability of semiconductors even at extreme temperatures. This is crucial for applications in aerospace, automotive, and industrial sectors where reliable operation under harsh conditions is critical.Secondly, quartz wafers exhibit lower electric leakage and reduced dielectric losses, resulting in more efficient power management and increased device lifespan. These characteristics make them particularly suited for power electronics and energy-efficient devices, where minimizing power loss is essential.Furthermore, quartz's exceptional mechanical properties, such as its high hardness and chemical resistance, enable the manufacturing of robust and long-lasting semiconductor devices. This durability facilitates cost reductions through longer device lifespans and reduced replacement or maintenance requirements.Quartz Wafers Corp.'s Innovative Manufacturing Technique:Quartz Wafers Corp.'s manufacturing process sets it apart from its competitors. The company utilizes a proprietary method that ensures the highest quality quartz wafers with precise thickness, flatness, and smoothness, being crucial factors in semiconductor fabrication. By leveraging advanced manufacturing techniques, Quartz Wafers Corp. can offer its customers superior products without compromising on cost-effectiveness.Applications of Quartz Wafers:Quartz wafers find applications in a wide range of industries. For instance, the demand for high-power electronics, such as inverters and converters, is rapidly growing. Quartz wafers' outstanding thermal and electrical properties make them an ideal choice for this market segment.Moreover, industries such as telecommunication, photonics, and optoelectronics will benefit from quartz wafers' superior optical transparency and exceptional UV stability. These attributes enable the production of high-quality optical components and devices, ensuring optimum performance in various light-related applications.Quartz wafers also hold promise for emerging technologies such as quantum computing and advanced sensor systems. Their unique material properties make them excellent candidates for applications requiring ultra-high precision and sensitivity.Conclusion:Quartz Wafers Corp.'s groundbreaking semiconductor manufacturing technology has the potential to revolutionize numerous industries. By leveraging the exceptional properties of quartz crystals, the company offers unparalleled substrates that enhance the performance, durability, and reliability of semiconductor devices. With applications ranging from power electronics to telecommunications and beyond, quartz wafers are poised to reshape the semiconductor landscape and unlock new possibilities in emerging technologies. As the demand for highly efficient and robust semiconductors continues to grow, Quartz Wafers Corp. stands at the forefront, ready to make a lasting impact.
Understanding the Importance of Substrate in the Semiconductor Industry
In today's fast-paced technological world, the semiconductor industry is constantly advancing with new discoveries and innovations. One of the newest advancements in the field of semiconductors is the substrate technology developed by a leading company in the industry.The unprecedented substrate technology developed by this company has revolutionized the way in which semiconductors are designed and manufactured. The substrate technology, which is used in a variety of electronic devices, enhances the performance of semiconductors by improving their speed, power efficiency, and overall functionality.Substrates are an essential component in the production of semiconductors, as they provide the foundation on which the semiconductor is built. The development of this new substrate technology, therefore, marks a major milestone in the industry, as it offers a significant improvement to the already existing substrate technology.The substrate technology developed by this company uses advanced materials and advanced manufacturing processes to create a highly efficient and high-performance substrate. The technology is based on a new type of substrate material that incorporates a number of cutting-edge design features, making it an ideal component for a range of electronic devices.The company's substrate technology has been specifically designed to meet the demands of modern electronics, such as smartphones, tablets, and power modules. With the increase in the number of electronic devices being used worldwide, there is now a greater demand for components that provide greater functionality and efficiency. This substrate technology is one such technology, offering improved performance, durability, and reliability in electronic devices.Furthermore, the new substrate technology provides a cost-effective solution for the manufacturing of semiconductors, enabling manufacturers to produce semiconductors more efficiently and at a lower cost. This technology, therefore, not only benefits the manufacturers but also benefits the end-users by driving down the cost of electronic devices.The company that has developed this revolutionary substrate technology has been in the semiconductor industry for over a decade. With a team of experienced professionals, they have made significant contributions to the development of a range of innovative semiconductor products.Their commitment to research and development has resulted in numerous breakthroughs in the field of semiconductor technology. Their latest development of the substrate technology is a testament to their expertise and dedication to creating products that meet the needs of the modern world.Looking to the future, this company continues to invest in research and development initiatives that will lead to further advancements in the field of semiconductor technology. As the industry advances, the company remains committed to developing innovative products that will set a new standard for performance, reliability, and functionality.Overall, the new substrate technology developed by this company is a significant advancement in the semiconductor industry. The technology is set to transform the way in which semiconductors are designed and manufactured, offering a cost-effective, high-performance solution that will benefit both manufacturers and end-users alike.With an experienced team of professionals and a commitment to research and development, this company is poised to remain at the forefront of the semiconductor industry for years to come. Their innovation and expertise continue to drive advancements in the field, creating products that will shape the future of technology.
Durable and Heat-Resistant Ceramic Plates for Industrial Applications
Alumina Ceramic Plate: A Revolution in Industrial ApplicationsIn recent years, industrial manufacturers have been facing numerous challenges in improving the performance and longevity of their products. In response to these demands, a revolutionary solution has emerged in the form of Alumina Ceramic Plates. With their exceptional properties and durability, these advanced ceramic plates have become the go-to choice for a wide range of industrial applications. In this article, we will explore the remarkable features of Alumina Ceramic Plates and delve into their potential applications across various industries.Alumina Ceramic Plates, often referred to as Al₂O₃ plates, are engineered using high-quality alumina powder, an aluminum-based material renowned for its excellent mechanical and thermal properties. Through a complex manufacturing process, the alumina powder is meticulously shaped, compacted, and sintered at high temperatures to form a solid ceramic plate. This process results in a dense, durable, and chemically inert material that can withstand extreme temperatures, harsh chemicals, and high mechanical stresses.One of the most notable features of Alumina Ceramic Plates is their exceptional hardness. With a Mohs hardness of 9, these plates are second only to diamonds in terms of hardness. This remarkable property ensures that the plates are highly resistant to wear and abrasion, making them ideal for applications where durability is paramount. Industries such as mining, construction, and material handling can benefit significantly from the use of Alumina Ceramic Plates in machinery components exposed to abrasive materials and heavy loads.Additionally, Alumina Ceramic Plates exhibit remarkable thermal stability, with an operating temperature range of up to 1500°C. This characteristic makes these plates ideal for use in high-temperature environments, allowing them to withstand extreme heat without any deterioration in their mechanical properties. Industries such as aerospace, automotive, and power generation can rely on Alumina Ceramic Plates to enhance the efficiency and longevity of their equipment operating under extreme temperature conditions.Furthermore, the excellent electrical insulation properties of Alumina Ceramic Plates make them invaluable in electrical and electronic applications. These plates possess high dielectric strength, low dielectric loss, and excellent thermal conductivity, making them ideal for use in manufacturing components for electronic devices, such as circuit boards and insulators. Additionally, their electrical insulation properties also make Alumina Ceramic Plates suitable for use in power distribution systems, where their ability to withstand high voltages ensures safe and reliable operations.In the medical field, Alumina Ceramic Plates have found exciting applications in orthopedic implants. Due to their biocompatibility, non-toxic nature, and resistance to corrosion, these plates are highly suitable for implantation within the human body. Alumina Ceramic Plates used in hip and knee replacements have demonstrated exceptional performance, improving the quality of life for patients and reducing the need for follow-up surgeries.Furthermore, Alumina Ceramic Plates are also making significant contributions to environmental sustainability. As a result of their exceptional mechanical and thermal properties, these plates enable manufacturers to develop more efficient and durable products. This, in turn, reduces the need for frequent replacements, leading to less waste generation and a reduced environmental impact.In conclusion, Alumina Ceramic Plates have revolutionized industrial applications across various sectors. Their exceptional mechanical properties, including high hardness, thermal stability, and electrical insulation, make them invaluable in industries ranging from mining to electronics. These plates also find exciting applications in the medical field and contribute to environmental sustainability. As industrial manufacturers continue to seek durable solutions to enhance their products' performance, Alumina Ceramic Plates undoubtedly stand as a game-changer in the industry.
Revolutionary Breakthrough: Researchers Discover the Power of a Single Metal Crystal
Single Metal Crystal Develops Groundbreaking Technology for the Industry [City], [Date] - Single Metal Crystal (SMC), a leading innovator in the technology field, has announced a groundbreaking advancement that is expected to revolutionize the industry. The company has developed a state-of-the-art technology that promises to enhance the performance and reliability of electronic devices.Founded by a group of passionate engineers and technologists, SMC has always been driven by the vision of creating cutting-edge solutions that address the challenges of modern technology. With a focus on research and development, the company has consistently delivered groundbreaking technologies that have set new standards in the industry.The recent breakthrough by SMC comes in the form of a revolutionary single metal crystal technology. This technology, which has been developed after years of meticulous research, offers unparalleled performance and reliability in electronic devices. It provides a significant improvement over traditional materials, leading to faster processing speeds, higher storage capacity, and more efficient energy usage.One of the key advantages of the single metal crystal technology is its scalability. SMC has successfully achieved scalable growth of single metal crystals, enabling mass production and widespread adoption of this technology. This breakthrough has the potential to transform a wide range of industries, including consumer electronics, telecommunications, automotive, and healthcare.The applications of this technology are virtually limitless. In consumer electronics, the single metal crystal technology can significantly improve the performance of smartphones, laptops, and gaming consoles, allowing for smoother and more immersive user experiences. In the telecommunications sector, the technology can enhance the speed and reliability of networks, leading to faster and more stable connections. Additionally, the automotive industry can benefit from this technology by improving the efficiency and performance of electric vehicles.Moreover, the healthcare sector stands to gain immensely from this innovative technology. Medical devices powered by the single metal crystal technology can revolutionize patient care by offering more accurate diagnostics and personalized treatments. Additionally, the improved performance and reliability of these devices can significantly enhance the overall efficiency of healthcare systems.Furthermore, SMC's commitment to sustainability is evident in their single metal crystal technology. By enabling more efficient energy usage in electronic devices, the technology contributes to reducing carbon emissions and conserving energy resources.The successful development of the single metal crystal technology is a testament to SMC's relentless pursuit of innovation. The company's dedicated team of scientists and engineers has worked tirelessly to overcome numerous challenges and turns this vision into reality."Our breakthrough single metal crystal technology will set new benchmarks for performance and reliability in the industry," said [Spokesperson], [Job Title] at SMC. "We are excited about the transformative potential of this technology and its ability to reshape various sectors of the economy. Our versatile technology will not only benefit individual consumers but also accelerate the progress of entire industries."With the unveiling of this groundbreaking technology, SMC has positioned itself at the forefront of the industry. The company is poised to revolutionize the electronic device landscape, bringing about a new era of enhanced performance and reliability.Looking ahead, SMC plans to further refine and optimize the single metal crystal technology, paving the way for even more advanced applications. The company aims to collaborate with industry partners to accelerate the adoption of this technology, ensuring its widespread availability and continued evolution.As Single Metal Crystal continues to push the boundaries of innovation, the technology world eagerly awaits the impact that their groundbreaking technology will bring. With its commitment to excellence and relentless pursuit of cutting-edge solutions, SMC is set to shape the future of the industry and improve the lives of millions worldwide.
New breakthrough in manufacturing process of computer processors using silicon wafer technology
Silicon Wafer Chips Revolutionize Semiconductor IndustryThe semiconductor industry, which lies at the heart of technological advancements, is constantly striving to push the boundaries of innovation. One of the most important components driving the progress of this industry is the silicon wafer chips, which serve as the foundation for manufacturing various electronic devices. In recent years, a number of leading companies have emerged in this market, one of which is [Company Name], a pioneering force that has been driving significant advancements and revolutionizing the production of silicon wafer chips.[Company Name] is a company at the forefront of semiconductor technology, dedicated to developing cutting-edge solutions that enable the production of advanced silicon wafer chips. With their commitment to innovation and harnessing the power of silicon-based technologies, [Company Name] has become a key player in the industry.Silicon wafer chips, commonly known as wafers, are thin slices of silicon that serve as the foundation for manufacturing integrated circuits (ICs), microchips, and other electronic components. These chips are crucial in powering a wide range of devices, including smartphones, computers, and automobiles, among others. The size and complexity of the chips have evolved significantly over the years, with continuous advancements in silicon wafer chip fabrication techniques leading to more powerful and efficient devices.[Company Name] has been instrumental in driving these advancements by developing innovative manufacturing processes and technologies. Their expertise lies in the production of high-quality silicon wafers, offering optimal performance and reliability. By leveraging state-of-the-art facilities and cutting-edge equipment, [Company Name] ensures the production of wafers with superior dimensional control, excellent surface quality, and high purity.The key to [Company Name]'s success lies in their relentless pursuit of innovation. They have consistently invested in research and development efforts to push the boundaries of silicon wafer chip technology. This has led to breakthroughs in wafer manufacturing techniques, such as epitaxial growth, chemical mechanical planarization, and lithography, among others. By incorporating these advancements into their manufacturing processes, [Company Name] has been able to improve the performance and functionality of their silicon wafer chips.Furthermore, [Company Name] recognizes the importance of sustainability in the semiconductor industry. They have implemented environmentally friendly practices in their wafer fabrication processes, ensuring minimal wastage and efficient use of resources. This commitment to sustainability not only benefits the environment but also allows them to deliver cost-effective solutions to their customers.The impact of [Company Name]'s silicon wafer chips goes beyond the manufacturing process. These chips have a profound influence on the overall performance of electronic devices. Through their continuous innovation, [Company Name] has enabled the development of smaller, faster, and more energy-efficient devices. This has positively impacted industries such as telecommunications, automotive, consumer electronics, and healthcare, among others.Looking into the future, [Company Name] is poised to maintain its leadership position in the silicon wafer chip market. They are investing in next-generation technologies, such as gallium nitride (GaN) and silicon carbide (SiC), which have the potential to revolutionize the semiconductor industry once again. These materials offer superior performance and efficiency compared to traditional silicon wafer chips, opening up new possibilities for various applications.In conclusion, [Company Name] has emerged as a prominent player in the semiconductor industry by revolutionizing the production of silicon wafer chips. With their commitment to innovation, sustainable practices, and continuous investment in research and development, they have set a new benchmark for the industry. Their silicon wafer chips have accelerated technological advancements, enabling the creation of smaller, faster, and more energy-efficient electronic devices. As they expand into next-generation technologies, [Company Name] is poised to shape the future of the semiconductor industry for years to come.
Revolutionizing Semiconductor Manufacturing: Unveiling the Groundbreaking Chemical Mechanical Planarization Process
Title: Advancements in Chemical Mechanical Planarization Process: Revolutionizing Material Polishing Introduction:In today's ever-evolving technological landscape, the demand for smaller, faster, and more efficient electronic devices continues to grow. This drives the need for more precise and superior manufacturing techniques. Chemical Mechanical Planarization (CMP) Process has emerged as a crucial technology in this respect. This article explores the potential of CMP process and its impact on various industries, focusing on its advancements without mentioning any specific brand.I. Understanding the CMP Process:The Chemical Mechanical Planarization (CMP) process is a cutting-edge method that allows the precise polishing and planarization of materials, predominantly used in the fabrication of integrated circuits (ICs). CMP involves the simultaneous action of chemical and mechanical forces to remove excess material from the surface, ensuring a smooth and uniform finish. It plays a fundamental role in improving various aspects of IC manufacturing, making it an essential part of the semiconductor industry.II. Advancements in CMP Process:1. Ultra-Planarization Capability:With the rapid advancements in semiconductor technology, the demand for ultra-planarized surfaces has become paramount. Recent advancements in CMP technology have enabled the development of ultra-precision polishing pads and slurries, resulting in superior planarization capabilities. This breakthrough allows for precise manufacturing of microelectronic devices, reducing surface variations and improving overall device performance.2. Material-Specific Polishing:To accommodate the diverse range of materials used in modern electronic devices, CMP processes are constantly evolving. Manufacturers are focusing on developing material-specific CMP slurries and pads to optimize the polishing efficiency for individual substances, including metals, dielectrics, and non-semiconductor materials. These material-specific CMP variations contribute to enhanced final device quality, reduced defects, and improved yield rates.3. Advanced Endpoint Detection:Accurate determination of the endpoint during the CMP process is critical to prevent over-polishing or under-polishing of the surface. Recent breakthroughs in CMP technology have introduced advanced endpoint detection mechanisms, such as optical interferometry, acoustic emissions, and electrical measurements. These technologies enable real-time monitoring, ensuring precise control and preventing damage to the underlying layers.III. Applications in the Semiconductor Industry:1. Integrated Circuit Manufacturing:The CMP process has become an indispensable technique in integrated circuit manufacturing. It enables the precise planarization of multiple layers, such as interconnects, interlayer dielectrics, barrier films, and metal contacts. The ability to achieve uniform surfaces results in improved electrical performance, reduced leakage currents, and enhanced device reliability.2. Advanced Packaging:As electronic devices become smaller and more complex, the demand for advanced packaging solutions increases. CMP processes are widely employed to polish and planarize materials used in packaging, such as through-silicon vias (TSVs), redistribution layers, and microbumps. The reliable CMP process ensures optimal electrical connections and increases the production yield of advanced packaging technologies.3. Optoelectronics and MEMS:CMP technology finds applications beyond traditional microelectronics. In the production of optoelectronics and microelectromechanical systems (MEMS), CMP plays a crucial role. The precise polishing and planarization of optical substrates, waveguides, and micro-mechanical systems contribute to improved device performance, optical clarity, and reliability.IV. Future Prospects:The constant advancements in CMP technology are poised to revolutionize the manufacturing industry further. Researchers and manufacturers are experimenting with novel materials, alternative polishing agents, and even greener chemical formulations to reduce environmental impact. Additionally, advancements in CMP equipment and automation are likely to improve process control, efficiency, and safety.Conclusion:Chemical Mechanical Planarization (CMP) Process is at the forefront of material polishing and planarization in the semiconductor industry. The advancements in CMP technology have proven instrumental in meeting the demands of faster, smaller, and more efficient electronic devices. By enabling ultra-planarization capabilities, material-specific polishing, and advanced endpoint detection, CMP processes drive better quality, yield rates, and reliability. As CMP continues to evolve in tandem with the ever-growing technological landscape, the future holds even greater promise for this vital manufacturing technique.
Sapphire Glass Windows: A Transparent Solution for Enhanced Durability and Clarity
Sapphire Glass Window: The Strength, Durability and Clarity You Need for Your HomeAre you looking for a window that’s built to withstand the test of time? Look no further than the Sapphire Glass Window, an innovative new product that’s set to revolutionize the industry.Made from sapphire, one of the hardest and most durable materials on the planet, these windows have an incredible level of strength and durability, making them the perfect choice for anyone who wants to invest in a product that’s built to last.But that’s not all – the Sapphire Glass Window also boasts a level of clarity that’s unmatched by other materials. This means that you’ll be able to enjoy stunning, uninterrupted views of the outside world, bringing the beauty of nature into your home.So, what makes sapphire such a special material? Well, for starters, it’s incredibly tough. In fact, sapphire is second only to diamond in terms of its hardness, making it highly resistant to scratches, chips, and other forms of damage.Moreover, sapphire is also incredibly strong, with a tensile strength that’s twice that of steel. This means that it can withstand greater forces and impacts without cracking or breaking, providing an added level of security and protection to your home.What’s more, sapphire is highly transparent, making it perfect for windows. It allows more light to pass through than other materials, which means that it can make your rooms brighter and more inviting. Plus, it’s highly resistant to yellowing, even after years of exposure to sunlight, ensuring that your windows will always look crystal-clear and new.But what about the cost, you might ask? While sapphire isn’t the cheapest material on the market, the longevity and durability of the Sapphire Glass Window make it a wise investment for anyone who wants to save money in the long run. Unlike other materials, sapphire doesn’t require frequent replacement or maintenance, which means that you’ll save money on repairs and replacements over the years.So, whether you’re building a new home or renovating an old one, the Sapphire Glass Window is a product that you won’t want to overlook. With its unparalleled strength, durability, and clarity, it’s the smart choice for anyone who wants to invest in a product that’s built to last.
A Guide to M-Plane Axis Sapphire Substrate for High-Performance Electronics
M-Plane Axis Sapphire Substrate Revolutionizes Technology IndustryIn a groundbreaking development, an innovative company, referred to as "Company X" (for confidentiality purposes), has introduced a cutting-edge M-Plane Axis Sapphire Substrate. This remarkable invention is set to revolutionize the technology industry, enabling more efficient and effective manufacturing processes for various electronic devices.The M-Plane Axis Sapphire Substrate is a thin, transparent crystalline material that acts as a foundation for the production of advanced electronic devices like LEDs, lasers, and power electronics. With its unique properties, this substrate offers significant advantages over traditional silicon-based substrates, promising superior performance and enhanced durability.One of the key benefits of the M-Plane Axis Sapphire Substrate is its exceptional heat dissipation properties. Electronic devices often generate heat during operation, leading to performance degradation and even failure. By utilizing this advanced substrate, manufacturers can effectively manage heat dissipation, thereby ensuring the longevity and reliability of their products.Additionally, the M-Plane Axis Sapphire Substrate offers exceptional electrical insulation characteristics. This quality is crucial for electronic devices, as it prevents unwanted electrical leakage and interference, ensuring optimal performance. With this substrate, manufacturers can produce devices that operate flawlessly, even in high-stress environments.Furthermore, this revolutionary substrate provides superior optical properties compared to traditional alternatives. Its crystal structure enables efficient light transmission, making it ideal for applications such as LEDs and lasers. As a result, devices utilizing the M-Plane Axis Sapphire Substrate can achieve higher brightness, better color rendering, and improved overall performance.The development of the M-Plane Axis Sapphire Substrate marks a significant advancement in the technology industry, as it offers a wide range of applications. LED displays and lighting systems, for instance, can greatly benefit from the exceptional light transmission properties of this substrate, leading to clearer and more vibrant visuals.Moreover, power electronics, such as power converters and inverters, can profit from its superior heat dissipation capabilities. By incorporating the M-Plane Axis Sapphire Substrate into these devices, manufacturers can ensure their efficient operation, reducing energy loss and enhancing overall reliability.Company X, the mastermind behind this groundbreaking invention, is dedicated to providing high-quality products and advancing technological innovation. With cutting-edge research facilities and a team of exceptional scientists and engineers, they strive to push the boundaries of what is possible in the technology sector.Recognizing the tremendous potential of the M-Plane Axis Sapphire Substrate, Company X has invested substantial resources into developing a state-of-the-art manufacturing process. This ensures the production of substrates that adhere to strict quality standards, allowing their customers to benefit from the exceptional properties of this innovative material.The introduction of the M-Plane Axis Sapphire Substrate could not have come at a better time, as the technology industry constantly seeks advancements to meet the growing demands of consumers. This revolutionary substrate promises to elevate the performance, durability, and overall user experience of various electronic devices, ushering in a new era of innovation.In conclusion, the M-Plane Axis Sapphire Substrate developed by Company X represents a significant breakthrough in the technology industry. With its exceptional heat dissipation, electrical insulation, and optical properties, this revolutionary substrate offers clear advantages over traditional alternatives. As manufacturers begin to incorporate this advanced material into their products, we can expect a new wave of electronic devices that are more efficient, reliable, and visually appealing.
Cutting-Edge Silicon Substrate: Revolutionizing Technology
Silicon Substrate Revolutionizes Semiconductor Manufacturing with Its Cutting-Edge TechnologySilicon Substrate, a leading provider of innovative and high-performance products in the semiconductor industry, has been making waves as it recently announced the launch of its latest offering. This new product utilizes cutting-edge technology that has the potential to revolutionize the way semiconductors are manufactured. The company's founder and CEO, John Smith, is excited to introduce this innovative product to the world.Silicon Substrate's latest offering delivers a comprehensive solution for semiconductor manufacturers seeking efficient, reliable and cost-effective solutions. The new product leads the market in performance and technology, positioning it at the forefront of the industry. This breakthrough technology is expected to improve manufacturing processes, increase productivity and enhance overall performance.The Silicon Substrate technology offers an unmatched level of precision that enables manufacturers to optimize the manufacturing process by minimizing wastage. This innovative technology minimizes processing errors, resulting in significant cost savings and improved quality control. John Smith, the CEO of Silicon Substrate, stated that, "our technology has the potential to boost the semiconductor industry by significantly cutting down on material wastage, and improving mass-production yields."Silicon Substrate products also offer superior physical and chemical properties that make them idealdenfor a wide range of applications that include aerospace, defense, power devices, photonics and biomedical. The superior thermal properties of Silicon Substrate's products enable manufacturers to produce highly efficient and reliable electronic products, which is critical in space and defense applications.Moreover, Silicon Substrate's products can operate in a wide range of temperatures and environments, making them ideal for harsh environments. The company's products can operate in temperatures from -200°C to 1200°C, making them ideal for a range of demanding applications, including high-power LEDs and power devices.Silicon Substrate's products are also environmentally friendly as the company uses a sustainable manufacturing methodology that reduces energy consumption and environmental waste. The company's patent-pending technology employs a water-based etching process that reduces the use of harsh chemicals, making its products safer to handle and manufacture.The Silicon Substrate technology is a game-changer for the semiconductor industry and has the potential to revolutionize the way we manufacture electronic products. The innovative technology provides manufacturers with an efficient and cost-effective solution that enhances product performance, improves manufacturing processes and reduces wastage.Silicon Substrate's innovative technology has caught the attention of many manufacturers in the semiconductor industry. The company has already gained recognition from several industry leaders, including Intel and Samsung. With its cutting-edge technology, the company is poised to lead the semiconductor industry into a new era of innovation and growth.In conclusion, Silicon Substrate's latest offering is a game-changer for the semiconductor industry. The company's innovative technology has the potential to revolutionize the way we manufacture electronic products. With superior physical and chemical properties and environmental sustainability, Silicon Substrate is positioned to lead the industry into a new era of growth and innovation. The technology is poised to gain wide adoption by manufacturers across the industry, allowing them to improve their manufacturing processes, reduce costs and achieve higher yields.
Emerging Advancements in Wafer Lithography: Unlocking New Possibilities for Semiconductor Development
Wafer Lithography Revolutionizes the Semiconductor Manufacturing ProcessAs technology continues to advance, so too has the demand for smaller and more powerful semiconductors. This has led to a surge in the development of new manufacturing techniques that can produce these advanced microchips. One of the latest innovations in the world of semiconductor manufacturing is wafer lithography, which has been making a big impact on the industry. Let’s take a closer look at this new technology.What is Wafer Lithography?Wafer lithography is a photolithography process used to pattern and etch thin films of material deposited onto a substrate. This technique involves using a light-sensitive material, called a photoresist, which is applied to the surface of a substrate. Light is then shone onto the photoresist through a mask, which contains the desired circuit pattern. The photoresist reacts to the light, becoming more or less soluble in certain regions depending on the dose of radiation received. This allows the material to be selectively removed from the substrate, leaving behind the desired pattern.The use of wafer lithography has revolutionized the way semiconductor manufacturers produce microchips. By using this process, manufacturers can create much smaller and more precise circuit patterns, which ultimately leads to more advanced and efficient semiconductors.One company that has been leading the way in the development of wafer lithography technology is {}. This innovative company has been at the forefront of semiconductor manufacturing for over a decade, and has played a major role in advancing this new manufacturing technique.How does {}’s Wafer Lithography Technology Work?The {} wafer lithography process uses a unique combination of advanced technologies to produce high-quality microchips. This process involves the use of a 193 nm excimer laser to pattern the photoresist, followed by a series of plasma etching steps to transfer the pattern onto the substrate.One of the key advantages of {}’s wafer lithography technology is its flexibility. The equipment can be configured to pattern a wide variety of materials, including silicon, quartz, and various types of polymers. This versatility allows manufacturers to produce a wide range of microchips, each with its own unique properties and capabilities.Another important feature of {}’s wafer lithography technology is its high throughput. The equipment is capable of patterning multiple wafers simultaneously, allowing manufacturers to produce large quantities of microchips quickly and efficiently. This high throughput makes {}’s equipment ideal for use in high-volume manufacturing environments.The Benefits of Wafer LithographyThe use of wafer lithography offers several advantages over traditional photolithography techniques. One major benefit is the ability to produce much smaller and more precise circuit patterns. This allows manufacturers to create more powerful and efficient semiconductors, which can be used in a wide range of applications, from smartphones to advanced computing systems.Another important benefit of wafer lithography is its flexibility. As mentioned earlier, the equipment can be configured to work with a wide range of materials, which means manufacturers can create a variety of microchip types. This versatility also makes wafer lithography a cost-effective manufacturing solution, as it eliminates the need for specialized equipment.ConclusionWafer lithography is an exciting new technology that is revolutionizing the semiconductor manufacturing process. Through its use of light-sensitive materials, manufacturers can create smaller and more precise circuit patterns, leading to more powerful and efficient microchips. {} has been at the forefront of this new technology, and its wafer lithography equipment offers a high-throughput, flexible solution for high-volume manufacturing environments. As technology continues to advance, wafer lithography is poised to play an increasingly important role in the semiconductor industry.
Quartz Wafers: A Potential Game-Changer in the Tech Industry
Title: The Pioneering Potential of Quartz Wafers in Semiconductor ManufacturingIntroduction:In the fast-paced world of semiconductor manufacturing, one company has emerged as a game-changer with its innovative quartz wafer technology. Quartz Wafers Corp., a leading provider of advanced substrate solutions, has introduced a groundbreaking production method that promises improved performance and cost-effectiveness for a variety of industries relying on semiconductors. This article delves into the potential of quartz wafers and their impact on the semiconductor landscape.Understanding Quartz Wafers:Quartz wafers are thin, disc-shaped substrates used as a base for fabricating semiconductor devices. Traditional silicon wafers have long dominated the industry, but Quartz Wafers Corp. aims to revolutionize the market by harnessing the unique properties of quartz crystals. Quartz is known for its exceptional electrical and thermal properties, making it an ideal material for manufacturing high-performance and reliable semiconductor devices.The Promise of Quartz:Quartz wafers offer numerous advantages over conventional silicon wafers. Firstly, quartz's high resistance to thermal stress ensures enhanced stability and reliability of semiconductors even at extreme temperatures. This is crucial for applications in aerospace, automotive, and industrial sectors where reliable operation under harsh conditions is critical.Secondly, quartz wafers exhibit lower electric leakage and reduced dielectric losses, resulting in more efficient power management and increased device lifespan. These characteristics make them particularly suited for power electronics and energy-efficient devices, where minimizing power loss is essential.Furthermore, quartz's exceptional mechanical properties, such as its high hardness and chemical resistance, enable the manufacturing of robust and long-lasting semiconductor devices. This durability facilitates cost reductions through longer device lifespans and reduced replacement or maintenance requirements.Quartz Wafers Corp.'s Innovative Manufacturing Technique:Quartz Wafers Corp.'s manufacturing process sets it apart from its competitors. The company utilizes a proprietary method that ensures the highest quality quartz wafers with precise thickness, flatness, and smoothness, being crucial factors in semiconductor fabrication. By leveraging advanced manufacturing techniques, Quartz Wafers Corp. can offer its customers superior products without compromising on cost-effectiveness.Applications of Quartz Wafers:Quartz wafers find applications in a wide range of industries. For instance, the demand for high-power electronics, such as inverters and converters, is rapidly growing. Quartz wafers' outstanding thermal and electrical properties make them an ideal choice for this market segment.Moreover, industries such as telecommunication, photonics, and optoelectronics will benefit from quartz wafers' superior optical transparency and exceptional UV stability. These attributes enable the production of high-quality optical components and devices, ensuring optimum performance in various light-related applications.Quartz wafers also hold promise for emerging technologies such as quantum computing and advanced sensor systems. Their unique material properties make them excellent candidates for applications requiring ultra-high precision and sensitivity.Conclusion:Quartz Wafers Corp.'s groundbreaking semiconductor manufacturing technology has the potential to revolutionize numerous industries. By leveraging the exceptional properties of quartz crystals, the company offers unparalleled substrates that enhance the performance, durability, and reliability of semiconductor devices. With applications ranging from power electronics to telecommunications and beyond, quartz wafers are poised to reshape the semiconductor landscape and unlock new possibilities in emerging technologies. As the demand for highly efficient and robust semiconductors continues to grow, Quartz Wafers Corp. stands at the forefront, ready to make a lasting impact.
Understanding the Importance of Substrate in the Semiconductor Industry
In today's fast-paced technological world, the semiconductor industry is constantly advancing with new discoveries and innovations. One of the newest advancements in the field of semiconductors is the substrate technology developed by a leading company in the industry.The unprecedented substrate technology developed by this company has revolutionized the way in which semiconductors are designed and manufactured. The substrate technology, which is used in a variety of electronic devices, enhances the performance of semiconductors by improving their speed, power efficiency, and overall functionality.Substrates are an essential component in the production of semiconductors, as they provide the foundation on which the semiconductor is built. The development of this new substrate technology, therefore, marks a major milestone in the industry, as it offers a significant improvement to the already existing substrate technology.The substrate technology developed by this company uses advanced materials and advanced manufacturing processes to create a highly efficient and high-performance substrate. The technology is based on a new type of substrate material that incorporates a number of cutting-edge design features, making it an ideal component for a range of electronic devices.The company's substrate technology has been specifically designed to meet the demands of modern electronics, such as smartphones, tablets, and power modules. With the increase in the number of electronic devices being used worldwide, there is now a greater demand for components that provide greater functionality and efficiency. This substrate technology is one such technology, offering improved performance, durability, and reliability in electronic devices.Furthermore, the new substrate technology provides a cost-effective solution for the manufacturing of semiconductors, enabling manufacturers to produce semiconductors more efficiently and at a lower cost. This technology, therefore, not only benefits the manufacturers but also benefits the end-users by driving down the cost of electronic devices.The company that has developed this revolutionary substrate technology has been in the semiconductor industry for over a decade. With a team of experienced professionals, they have made significant contributions to the development of a range of innovative semiconductor products.Their commitment to research and development has resulted in numerous breakthroughs in the field of semiconductor technology. Their latest development of the substrate technology is a testament to their expertise and dedication to creating products that meet the needs of the modern world.Looking to the future, this company continues to invest in research and development initiatives that will lead to further advancements in the field of semiconductor technology. As the industry advances, the company remains committed to developing innovative products that will set a new standard for performance, reliability, and functionality.Overall, the new substrate technology developed by this company is a significant advancement in the semiconductor industry. The technology is set to transform the way in which semiconductors are designed and manufactured, offering a cost-effective, high-performance solution that will benefit both manufacturers and end-users alike.With an experienced team of professionals and a commitment to research and development, this company is poised to remain at the forefront of the semiconductor industry for years to come. Their innovation and expertise continue to drive advancements in the field, creating products that will shape the future of technology.